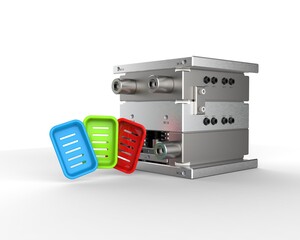
طراحی و ساخت قالب های صنعتی اولین مرحله از قالب سازی صنعتی در شرکت فن آورپلاستیک است. تولید کنندگان برای طراحی دقیق این الگوهای مدرن صنعتی معمولاً از نرمافزارهای به روز دنیا استفاده می کنند. پس از اتمام طراحی، با روشهای مختلف ساخت انواع قالب های صنعتی با مختلفی چون مواد اولیه فلزی و پلاستیکی انجام می گیرد.
طراحی و ساخت انواع قالب های صنعتی
در مقاله قبلی بررسی کردیم قالب های صنعتی چیست؟ و کاربردهای این قالب ها را به طور مفصل بررسی کردیم. زمانی که یک قطعه صنعتی نیاز به تولید در تعداد بالا داشته باشد، از قطعه یک قالب صنعتی (محفظه یا اولگو) درست مشابه با قطعه اصلی تهیه می شود. برای سفارش انواع محفظه ها اولین مرحله ای که انجام می شود طراحی قالب است. تولیدکنندگان برای طراحی دقیق معمولاً از نرم افزارهای به روز دنیا استفاده می کنند تا خطای این مرحله به حداقل مقدار خود برسد. هر چه خطا در مرحله طراحی پایین تر باشد محصول نهایی با دقت و کیفیت بالاتری تولید می شود. پس از اتمام طراحی، با روش های مختلف و بسته به نیاز کارفرما سعی می شود ساخت قالب با مواد اولیه مناسب با پروژه انجام می گیرد.
شرکت قالب سازی فن آور پلاستیک تولید کننده این الگوها و محفظه ها با جدیدترین دستگاههای روز دنیا است. این شرکت آمده است تا هر ایده ای را به محصول تبدیل کند. فروش قالب های صنعتی حرفه ای تخصص ماست. روش هایی که برای طراحی ساخت قالب در شرکت فن آور پلاستیک تولید می شود بسیار متنوع است که این تنوع کمک می کند تا برای هر پروژه ای این شرکت بهترین گزینه باشد. انواع روش های طراحی و ساخت قالب در این شرکت به شرح زیر است که به بررسی تک تک این روش ها می پردازیم:
- قالب سازی پلاستیک
- طراحی و ساخت قالب های دایکاست
- اکستروژن
- قالب های فلزی
طراحی و ساخت انواع قالب های پلاستیک
یکی از پر کاربرد ترین و متنوع ترین روش های ساخت قطعه پلاستیکی، با مواد اولیه پلاستیکی است. قالب سازی پلاستیک در تولید انواع قطعات پلاستیکی و محصولات پر مصرفی صنعتی به عنوان یکی از بخشهای حیاتی تولید، نقش بسیار مهمی ایفا میکند. ساخت قالب های صنعتی در قالبسازی پلاستیک به منظور تولید انبوه و همچنین تولید قطعات دقیق و یکسان به کار میروند.
طراحی قالب صنعتی در قالب سازی پلاستیک
قالب سازی پلاستیک به روش های زیادی انجام می شود که پرکاربردترین آن با استفاده از روش تزریق پلاستیک انجام می گیرد. فرایند قالب تزریق پلاستیک با طراحی شروع می شود. برای طراحی از نرم افزار های مختلفی چون نرم افزار مهندسی CATIA استفاده می گردد.
قالب های صنعتی که در قالب سازی پلاستیک استفاده می شوند به عنوان قالب هایی با قابلیت تزریق مواد اولیه پلاستیکی برای تولید قطعات صنعتی مختلف به کار میروند. این قالب ها توانایی تولید قطعات با دقت بالا، سرعت بالا و همچنین تیراژ بالا را دارا میباشد که ین ویژگی ها حتما صرفه جویی در قیمت را نیز به همراه دارد. در نتیجه، تولیدکنندگان میتوانند با استفاده از قالب های صنعتی، قطعات با کیفیت و با قیمت مناسب تولید نمایند.
در طراحی قالب های صنعتی در قالبسازی پلاستیک، چندین نکته بسیار مهم وجود دارد که باید مورد توجه قرار گیرد. این نکات عبارتند از انتخاب مواد اولیه قالب و مواد اولیه تزریق، هندسه قطعه و فرآیندهای ساخت قالب و تولید قطعه. بهتر است طراحان قالب همراه با سازندگان قالب همکاری کنند تا قالب هایی با کیفیت و مناسب برای تولید قطعات صنعتی تولید کنند.
فرآیند ساخت قالب های صنعتی
فرآیند ساخت شامل چندین مرحله است. ابتدا، قالب با استفاده از تکنیکهای ماشین کاری تولید میشود. در این مرحله، دقت و کیفیت تولید قالب بسیار مهم است که در مرحله بازرسی کیفی قالب صحت و سلامت آنها اطمینان حاصل شود.
در ساخت قالب های صنعتی در قالبسازی پلاستیک، از مواد مختلفی استفاده میشود. برخی از مواد متداول شامل فولاد و آلیاژهای خاصی از فولاد، آلومینیوم و فولاد ضد زنگ میباشند. انتخاب ماده مناسب برای ساخت قالب بستگی به نوع قطعه، دقت مورد نیاز و مقدار تولید (تیراژ یا تناژ) دارد.
مواد اولیه پلاستیک در ساخت قطعه صنعتی
بعد از ساخت قالب نوبت به ساخت قطعه به کمک تزریق پلاستیک می رسد. برای تولید قطعه پلاستیکی صنعتی به کمک قالب تزریق پلاستیک از دو ماده اولیه استفاده می شود:
-
ترموپلاستیک
-
ترموست (باکالیت)
گروه ترموپلاستیک ها: یا گرمانرم ها، موادی هستند که بر اثر حرارت خمیده گشته و با گرم شدن میزان گرما سختی خود را ازدست میدهند و نرم می شوند. با افزایش دما و حرارت، تغییرات شیمیایی در این گروه صورت نمی گیرد و بعد از تزریق، شکل محفظه قالب را به خود میگیرند. در مرحله تزریق، ماده اولیه ترموپلاست گرم محفظه را پر می کند و این ماده گرما دیده در محفظه سرد شده که طی این فرایند مواد به شکل و فرم محفظه درمی آید و سخت میشود.
گروه ترموست: یا باکالیت یا گرما سخت ها که این گروه بر اثر حرارت دیدن سخت میشوند و حرارت باعث تغییرات شیمیایی در این مواد می شوند. در این مواد اولیه، قالب تزریق پلاستیک در حالت سرد می باشد و مواد نیز سرد هستند. بعد از تزریق، محفظه را تحت حرارت قرار میدهند و مواد شکل و فرم محفظه را به خود می گیرد و سخت می شود. مواد ترموست یا دورپلاست ها تحت تأثیر فشار و حرارت 170 درجه سانتی گراد تولید می شوند. در ابتدای فرایند این مواد اولیه نرم شده و به حالت پلاستیک درمیآیند ولی بعد از مدتی سخت میشوند. خصوصیت اصلی این مواد آن است که پس از سخت شدن مجدداً قابل نرم شدن و استفاده مجدد نیستند و در هیچ نوع ماده حلالی قابل حل نمی باشند و پس از سخت شدن، تغییرات شیمیایی در آنها روی می دهد که به طور اجمالی این مباحث به تعریف قالبسازی مدرن میپردازد.
طراحی و ساخت قالب های دایکاست
قالب های صنعتی دایکست امکان تولید قطعات فلزی را در صنعت فراهم کرده است. در این فرایند، که یک نوع قالب سازی به روش ریخته گری است، مواد مذاب (که می توانند موادی مانند آلومینیوم و مس و غیره باشند) تحت فشار معینی به محفظه یک تکه یا چند تکه هدایت می شود. این روش بسیار شبیه به روش تزریق پلاستیک است ولی ماده اولیه جهت تزریق متفاوت است. با استفاده از این روش، قطعات صنعتی با دقت بالا و فرم های پیچیده و تمیز را می توان تولید نمود.
این روش برای صنایعی مانند خودروسازی، هوافضا و الکترونیک مصرفی بسیار حائز اهمیت هستند که دقت و کارآیی در آنها امری حیاتی است.
قالب سازی دایکاست، همچنین به عنوان قالب ماتریس یا ابزار دایکست شناخته میشوند، ابزارهای ویژهای که در فرآیند دایکست استفاده میشوند. دایکست شامل تزریق مواد فلزی مذاب به داخل یک مجرای قالب با فشار بالا است، که مواد مذاب در آن سفید میشود و شکل قالب را به خود میگیرد. محصول حاصل، قطعهای فلزی با دقت و کیفیت بالا خواهد بود.
خود قالب در صنعت قالب سازی دایکاست معمولاً از مواد ماندگاری مانند فولاد، آلومینیوم یا آلیاژهای روی و چندان تخریبپذیر ساخته میشوند و قادرند با فشارها و دماهای بالای مرتبط با فرآیند دایکست بدون خرابی مقاومت کنند. این قالبها برای ایجاد شکلها و ساختارهای پیچیده با تحملهای بالا به صورت دقیق طراحی و ساخته شدهاند تا هماهنگی و دقت در محصولات نهایی را تضمین کنند.
مواد اولیه که در ساخت قالبهای دایکاست استفاده میشوند
-
فولاد
-
آلومینیوم
-
روی
-
سایر مواد: مانند آلیاژهای دیگر فلزی، سرامیک یا مواد مرکب تا به نیازهای خاص فرآیند و محصولات پاسخ دهند.
هر کدام از این ماده های اولیه بسته به نوع قطعه تولیدی و میزان سفارش بستگی دارد.
مراحل طراحی و ساخت قالب دایکاست
دایکست یک فرآیند پیچیده است که شامل چند مرحله است. در ادامه، مراحل ساخت قالب دایکست را بررسی میکنیم:
طراحی قالب:
ابتدا، قالب بهصورت دقیق طراحی میشود. نرمافزارهای طراحی سهبعدی و شبیهسازی انجام میشوند تا شکل و ابعاد دقیق قالب و قطعه نهایی مشخص شوند.
ساخت قالب:
پس از طراحی، قالب ساخته میشود. این شامل ماشینکاری قطعات قالب، تراشکاری، حفر و برش است. تجهیزات پیشرفته مانند CNC (کنترل عددی کامپیوتری) و الکترو EDM (الکتروآبشارسنگ) در این فرآیند استفاده میشوند.
تجمیع قالب:
قطعات ساخته شده قالب، تجمیع میشوند و قالب نهایی شکل میگیرد. این مرحله شامل جوشکاری، پیچگذاری و تراشکاری دقیق است.
آزمایش و تنظیمات:
قالب نهایی آزمایش میشود و تنظیمات لازم برای بهینهسازی فرآیند دایکست انجام میشود. این شامل تستهای ریزساختار، اندازهگیری دقیق ابعاد و تنظیمات دما و فشار است.
طراحی و ساخت قالب اکستروژن صنعتی
قالب سازی اکستروژن یک فرآیند تولید قطعات فلزی است که در آن مواد فلزی مانند آلومینیوم، از طریق یک قالب به شکل یکنواختی فشرده و از طریق یک دیسک فشار داده میشود. این فرآیند از قدیمیترین و محبوبترین روشها برای تولید قطعات فلزی استفاده میشود.
مکانیسم کلی قالب سازی اکستروژن عبارت از یک مارپیچ که حرکت خود را از یک موتور و گیربکس می گیرد و در سیلندری که به وسیله گرم کن های خارجی گرم می شود حرکت می کند. در این روش مواد اولیه به صورت دانه از قیف داخل دستگاه به داخل محفظه ریخته می شوند.
بعد از ذوب شدن مواد با فشار از درون فرم اکستروژن عبور کرده و به مرور سرد می شوند و در حین سرد شدن، شکل فرم قالب اکستروژن را به خود می گیرد. این روش برای تولید قطعاتی مانند سیم ها، میله ها، لوله ها، ورق ها و … استفاده می شود.
برای ساخت قالب های اکستروژن از مواد مختلفی نظیر فولاد و آلومینیوم استفاده می شود. اما آلومینیوم نسب به فولاد در روش اکستروژن کاربرد بیشتری دارد در حدی که این قالب ها به قالب اکستروژن آلومینیوم معروف هستند.
مزایای قالب اکستروژن که با آلومینیوم ساخته شده است
قالبهای اکستروژن آلومینیوم دارای مزایای فراوانی هستند. این قالبها قادر به تولید قطعات با شکلهای مختلف و پیچیده هستند. آلومینیوم یک فلز سبک و با دوام است و قالب های اکستروژن آلمینیوم قطعاتی را تولید میکنند که سبک و همزمان مقاومت بالایی دارند. این قالبها در صنایع مختلفی مانند خودروسازی، هوافضا، الکترونیک و ساختمانسازی استفاده میشوند.
قالبهای اکستروژن آلمینیوم به شکلها و اندازههای مختلفی تولید میشوند. برخی از انواع قالبهای رایج شامل قالبهای پیشرفته، قالبهای متقارن، قالبهای مجرد و قالبهای مشخصهدار هستند. هر نوع قالب برای استفاده در صنایع و کاربردهای خاصی مناسب است و بسته به نیاز، انتخاب میشود.
حال که راجع به جنس بدنه قالب اکستروژن صحبت کردیم، لازم می دانم انتهای مقاله را با موضوع جنس قالب های فلزی تمام کنیم.
طراحی و ساخت قالب های صنعتی فلزی
در تولید انواع قالب های صنعتی که برای تولید قطعات فلزی هستند از روش های مختلف ریخته گری استفاده می شود، از طرفی دیگر از انواع فلزها نیز برای ساخت این محفظه ها استفاده می شود.
اما روش های ساخت قالب های صنعتی فلزی نیز با یکدیگر متفاوت است. در ادامه برخی از این روش ها را به صورت مختصر بررسی کرده و در یک مقاله دیگر به طور مفصل بررسی می کنیم
1- قالب سازی سنبه و ماتریس:
این فرایند روشی است که در آن محفظه دارای 2 قسمت فرورفتگی و برآمدگی است و برای هدف یابی متفاوتی از قبیل:
برش- خم- کشش- فرم و غیره استفاده می شوند
2- برش:
بریده شدن قطعه، بین دو لبه ی برنده ی محفظه را قیچی شدن می گویند. این فرایند بدین ترتیب است که ابتدا فشار – از قسمت بالایی حفره (سنبه) بر قطعه وارد شده و معادل آن نیروی استحکام کشش قطعه در جهت مخالف آن، عکس العمل نشان می دهد تا حدی که نیروی فشار فوقانی بیش از نیروی استحکام کششی شود. در این حالت قطعه کنده می شود.
3- خمش:
خمش، پیچ خوردگی هماهنگ و هارمونیک ماده به دور محوری صاف و مستقیم است که بر روی صفحه خنثی بوده و بر راستای طولی ورق عمود است. در این روش کشش باعث دگرگونی دانه بندی ماده می شود.
4- کشش:
کشش نوعی فلز کاری است که در آن ورق سرد یا قطعه ای با برش محصور در داخل یک ظرف خالی (ماتریس ) بدون ایجاد چروک یا شکستگی فرم داده می شود. فرم های مختلف ممکن است سیلندری جعبه ای شکل با دیواره های صاف یا دیواره های خمیده یا ترکیبی از این دو باشد.
5- فرم:
فرم دادن، نوعی خمش است. ایجاد سنبه و ماتریس بر حسب نوع قطعه و فرم آن با احتساب حالت مزیت و غلبه بر آن در فلزات را نیز شامل می شود. فرآیند فرم کاری از جمله فنون است که برای ایجاد شکل های پیچیده به کار می رود. تفاوت این فرآیند با کشش از نظر میزان و نوع تغییر شکلی است که ایجاد می شود.